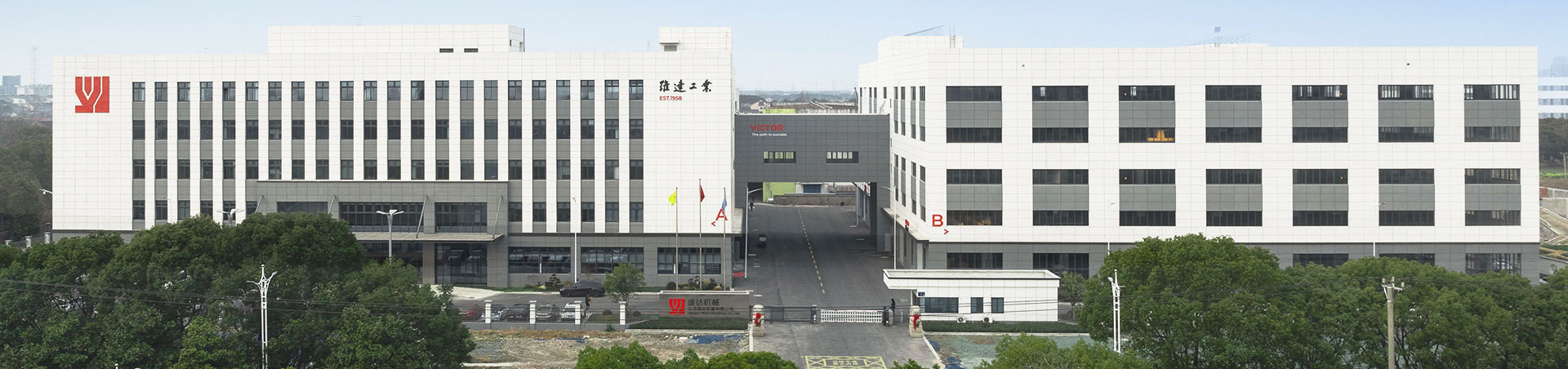
Product Application
Advantage
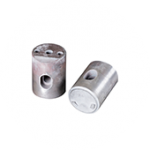
Special designed single crossbar dual-cylinder balance clamping system,for fast opening and closing mold while ensuring uniform distribution.
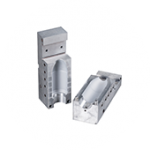
Unique rotating mechanism design, and equipped with automatic lubrication system,ensure rotation precision be consistent.
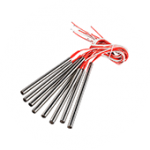
Alternative efficient plasticizing mixing screw, optimization of the injection unt,improve the injection stability and accuracy.
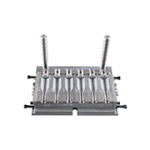
Equipped with electro-hydraulic servo system, the machine is running stable, low noise, high response and energy saving of 25% to 45%.
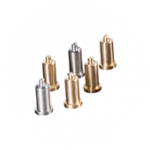
Screw optimization design, clamp screw head assembly, with good plasticizing ability, wear resistance.
Processing principle
Injection Blow Molding Machine is a special designed machine with a rotarythree station index, after perform injection the perform will be sent to beblow station, then stripped for next processing like washing or filling neededby conveyor. It is suitable for PE, PP, PS, SAN, EVA, COC, PEEK, TPU PETG,PET etc material, bottles volume various from lml-I000ml.The l.B.M bottlehas a perfect neck finish and strict body thickness and weight, it is good forhigh quality packing like pharmaceutical, cosmetic, house holding,foodproducts packing industrial.
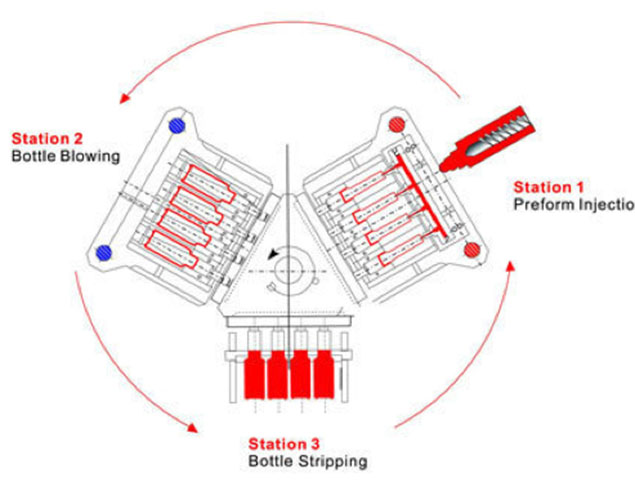
Parameter Table
Preform system | Unit | MSZ30 | MSZ50H | MSZ50S | MSZ70 | MSZ70S | MSZ95S | MSZ135 |
Screw diameter | mm | 40 | 50 | 50 | 55 | 55 | 65 | 70 |
Screw L/D | L/D | 23:1 | 23:1 | 23:1 | 23:1 | 23:1 | 23:1 | 23:1 |
Shot volume | cm3 | 200 | 392 | 392 | 475 | 475 | 839 | 1077 |
Injection weight(HDPE) | g | 190 | 372 | 372 | 450 | 450 | 795 | 1020 |
Max.Screw speed | rpm | 10-225 | 10-235 | 10-235 | 10-235 | 10-235 | 10-235 | 10-235 |
Heating capacity | KW | 8.3 | 10 | 10 | 10.8 | 10.8 | 12.6 | 15 |
No.of heating zone | Qty | 3+N | 4+N | 4+N | 3+N | 3+N | 3+N | 3+N |
Clamping system | ||||||||
Clamping force of preform | KN | 289.7 | 504 | 528 | 742 | 712 | 1008 | 1344 |
Clamping force of blowing | KN | 46.7 | 89 | 93.4 | 89 | 107.7 | 221 | 235 |
Opening stroke of mold planten | mm | 120 | 130 | 165 | 140 | 165 | 155 | 155 |
Lifting H of rotary table | mm | 65 | 70 | 80 | 70 | 80 | 75 | 75 |
Max.Platen size(L×W) | mm | 400×270 | 560×390 | 560×390 | 800×390 | 800×390 | 900×480 | 1400×500 |
Min.mold thickness(H) | mm | 180 | 240 | 240 | 280 | 280 | 280 | 280 |
Heating capacity of mould | KW | 3 | 3.6 | 3.6 | 6 | 10 | 10 | 10 |
Stripping system | ||||||||
Stripping stroke | mm | 220 | 270 | 270 | 240 | 295 | 260 | 260 |
Dry cycle | sec | 3.5 | 3.5 | 2 | 3.5 | 2.1 | 3 | 4.5 |
Driving system | ||||||||
Motor power | KW | 18.2 | 23 | 23 | 39.4 | 31 | 26+26 | 39.4+39.4 |
Hydraulic pressure | Mpa | 14 | 14 | 14 | 14 | 14 | 14 | 14 |
Product range | ||||||||
Suitable bottle volume | ml | 5-800 | 5-800 | 5-800 | 5-800 | 5-800 | 5-800 | 5-800 |
MAX.bottle height | mm | ≤190 | ≤200 | ≤200 | ≤200 | ≤200 | ≤220 | ≤220 |
Max.Dia.of bottle | mm | ≤100 | ≤100 | ≤100 | ≤100 | ≤100 | ≤100 | ≤100 |
Other | ||||||||
Compressed air pressure | Mpa | 1 | 1 | 1 | 1 | 1 | 1 | 1 |
Compressed air discharge | m3/mm | ≥0.7 | ≥0.7 | ≥0.7 | ≥0.8 | ≥0.8 | ≥1 | ≥1.2 |
Cooling water flow | m3/h | 3 | 4 | 4 | 5 | 5 | 6 | 6 |
Total rated power with mold heating | KW | 29.5 | 36.6 | 36.6 | 56.2 | 59 | 75.6 | 106.8 |
Dimension(L×W×H) | M | 3.56×1.25×2.25 | 4.11×1.57×2.5 | 4.11×1.57×2.5 | 4.1×1.78×2.6 | 4.39×1.91×2.54 | 5.0×2.0×2.6 | 6.0×2.5×2.6 |
Net weinght | ton | 4 | 5.7 | 5.7 | 9 | 9 | 12 | 15 |